
1. 案例概述
由本平台组态软件开发的《锅炉燃烧智能分析系统》于2017年在多台350MW超临界电站机组开始运行,系统主要解决锅炉燃烧不均问题,主要对炉膛各层燃烧区域、水冷壁温、过热器及再热器壁温进行偏差和寿命管理;对切圆偏差、风煤比率、磨煤机动态特性、煤质状态、结焦状态、各部漏风等实时进行监测分析;通过模型核算,间接计算出炉膛中心温度、出口温度、还原性气氛、结焦结渣指数、风机运行特性、煤质热值特性、煤耗等指标,对产生的偏差进行分析和状态监测。
智能分析系统在软件完善的基础上安装了部分测量元件,主要测量水冷壁四墙还原性及烟温偏差,测量省煤器出口烟气流场及温度偏差分布状态,供锅炉运行人员进行深层精细调整,供管理部门安全经济性预测以及适应灵活性改造的低负荷稳燃的调整监测。2018年新增加了对节能分析的统计优化:利用大数据模型算法,对历史数据、设计数据及性能试验数据进行比对,给运行人员提供更清晰的控制思路和快速解决途径。
智能分析系统下一步的主要工作是将模型系统纳入到热工闭环燃烧控制中,即对所有二次风门进行自动调节,通过完善和优化运行指导,该智能系统逐渐成为现场运行人员的好帮手,为未来工业大数据及工业人工智能的发展提供应用平台,平台的显示屏安装在现场主控制室中,供操作人员随时进行燃烧调整分析。
智能分析系统通过对锅炉燃烧及工质流动的数学模型分析,根据质量平衡、热量平衡的原则,通过模型的收敛计算,核算出锅炉燃烧和烟气流动中的深层次节能参数,使运行人员更深入和更直观地监测锅炉各项动态参数和指标,比如锅炉效率的变化,漏风和单耗的变化,汽机热耗的变化,供电或发电煤耗的实时变化等,这些指标都可以通过平台模型分析或试验标定构建出来,供电厂从更高层次来分析锅炉的经济特性。
2. 硬件系统
平台的参数主要来源于现场DCS系统,这些参数是锅炉燃烧分析和运行诊断的重要计算依据,参数从DCS系统引出后,通过多点数据取舍的优化算法进行修正。为了保证现场DCS系统不受任何通讯干扰,平台在DCS系统接口工作站后端的单向网闸出口安装千兆级的工业数据交换机,在保证进入SIS系统数据安全条件下,将数据通过交换机全部引入到本平台工控机中。
电站DCS接口工作站的输出数据方式是根据电厂组态数据协议制定的。引入本平台之前,必须安装单向通讯网闸和千兆级工业交换机,主要目的是保证不对现有数据通讯产生任何干扰,同时保证对引出到SIS系统的通讯速率、带宽、数据格式等不做任何改变。平台需要在现场新安装的主要设备是单向数据通讯网闸、千兆级工业交换机、工控机、显示屏及单根网络总线。
在省煤器出口两侧烟道截面上,采用网格法进行气体取样分析,安装取样测点之前,选进行相关锅炉试验标准进行两侧烟道截面的网格标定和流场代表点选取工作。省煤器出口单侧烟道选取的测点为32点,从8根取样管引出,接入到气体分析的采样变送器,通过CAN和RS485总线将数据传送到平台工控机中。
在水冷壁上部燃烬层对氮氧化物和还原性气体进行监测,测点安装在燃烬层下方垂直管间鳍片上,钻孔引出,引出管的安装位置处于还原性最强的四侧墙壁,测点数量根据电厂煤种情况制定,原则上不少于16个点的取样实时测量。
通过取样监测系统,实现对烟气成分(主要是O2、CO等,根据电厂炉膛燃烧条件制定)的精确采样及分析。取样单元、样气处理单元、反吹单元和变送器等测量设备,应能够有效的应用于现场各种复杂工况条件,结构合理,性能稳定,响应时间快,操作简便,维护量小。这些采样设备是平台系统的重要组成部分和核心技术。
燃煤锅炉烟道中进行烟气取样测量时,取样探头是重要环节,能经受热气流冲刷、烟气腐蚀、烟尘堵塞等恶劣条件的影响。配置是否正确直接关系到取样系统能否正常稳定运行,这些配置方案可以根据电厂的要求实际订制。在省煤器出口两侧烟道截面上共取64个网络格点,通过8根管引出进行取样。这些测量参数主要为精准判断从炉膛出口的烟气层流中的局部缺氧状态,为炉膛的偏烧及燃烧的不均性提供模型计算的数值监测及修正方法,为运行人员对炉内燃烧状态提供更详细的独立监测手段。
下面是现场依赖本组态平台开发的《锅炉燃烧智能分析系统》主要运行画面,仅供参考。
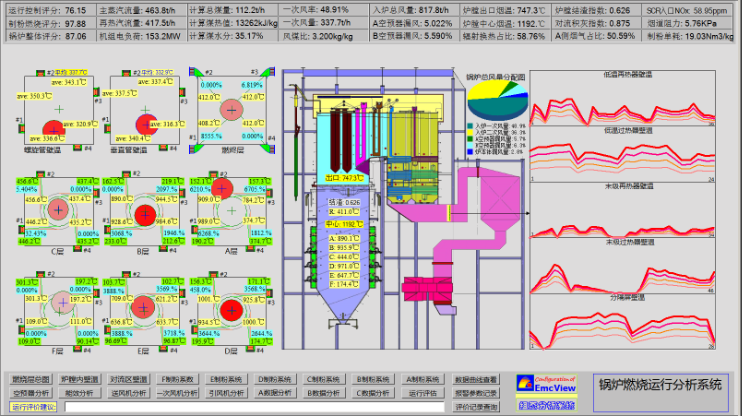
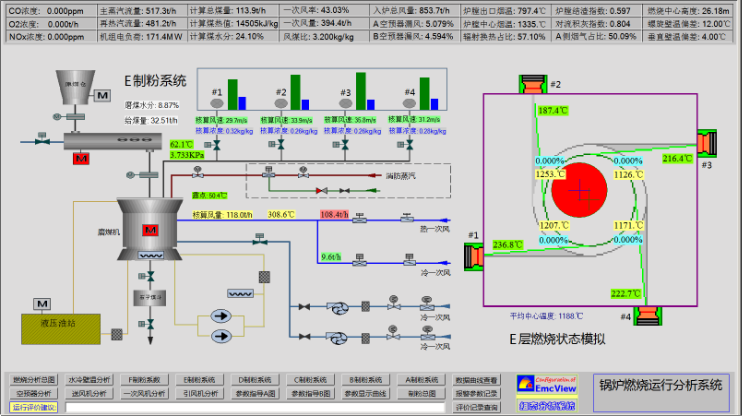
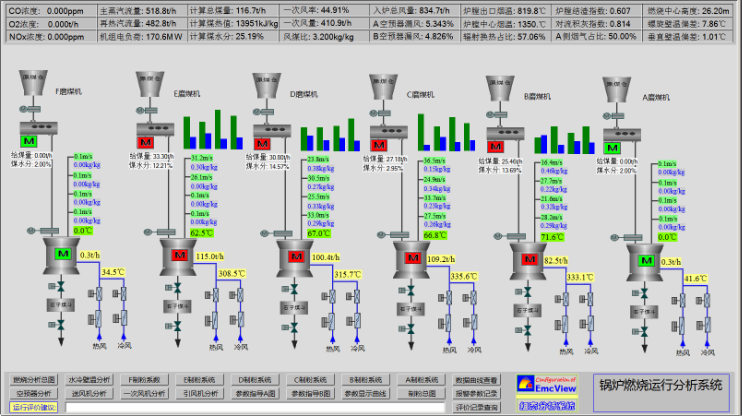
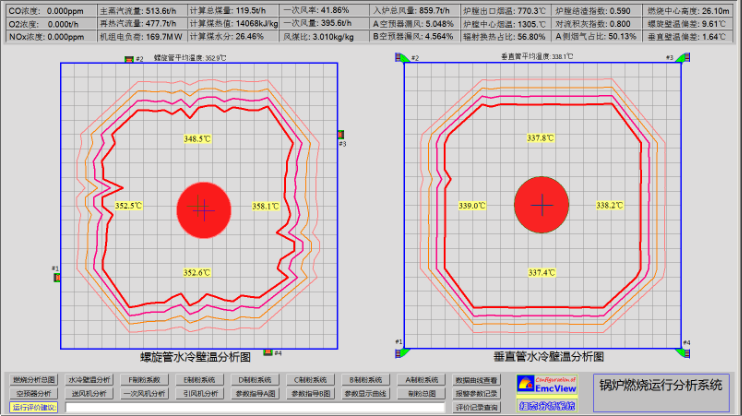
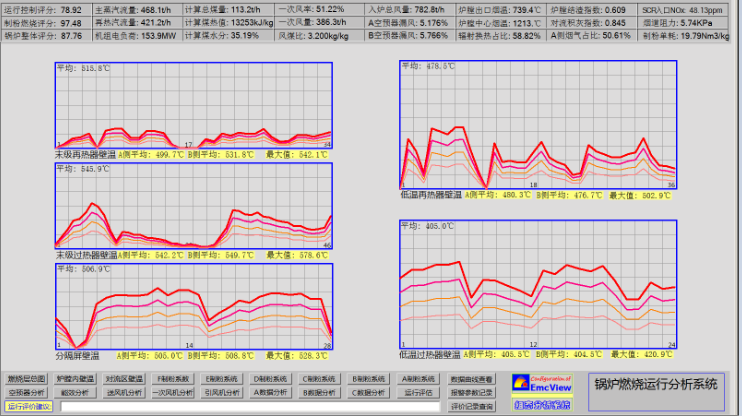
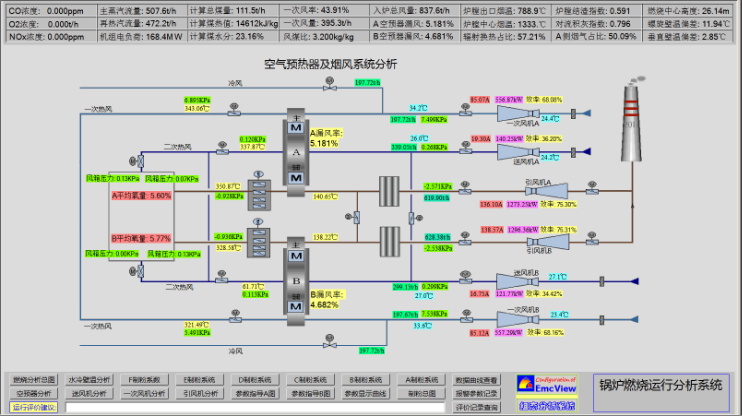
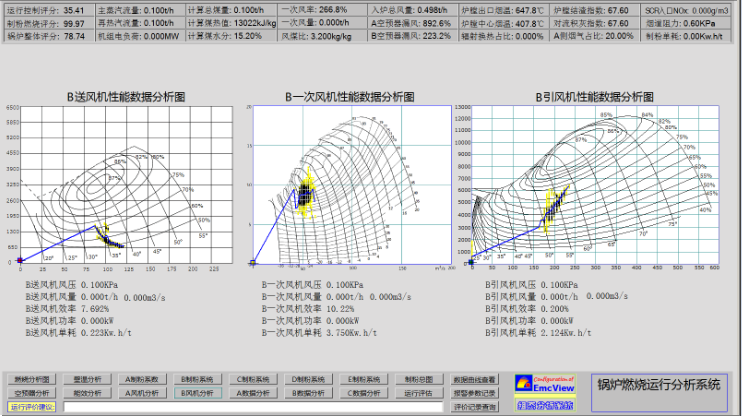
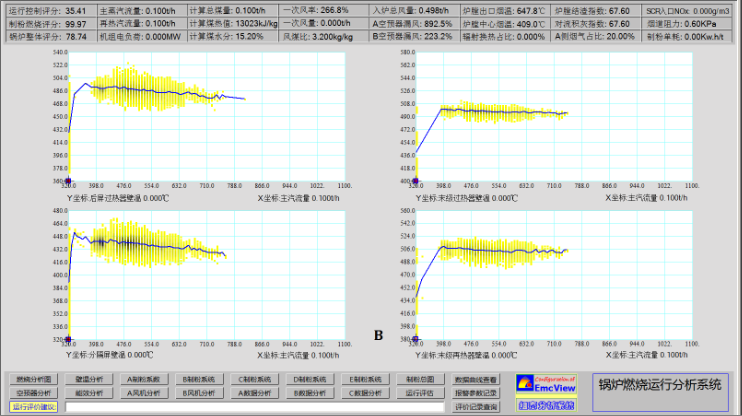
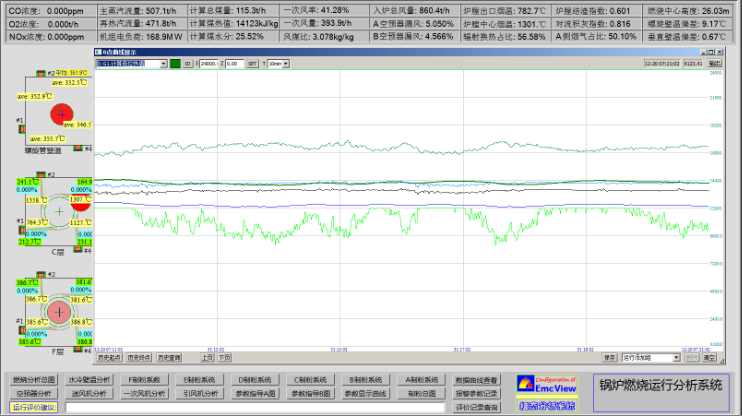
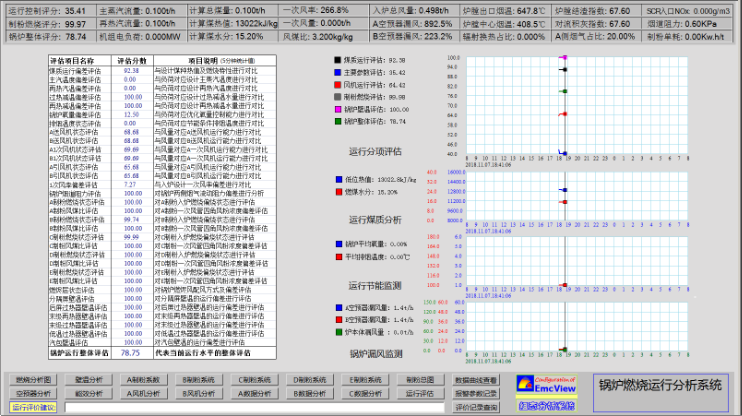